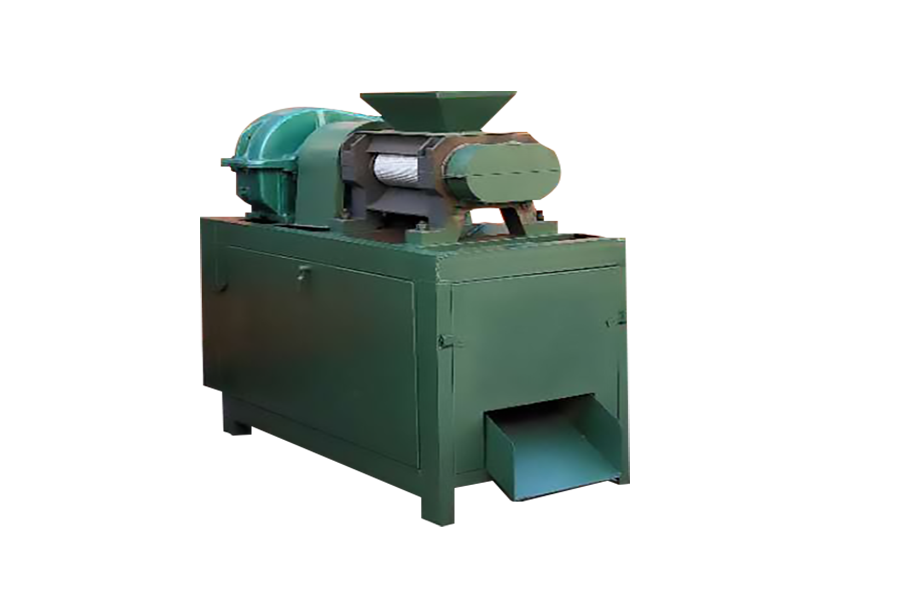
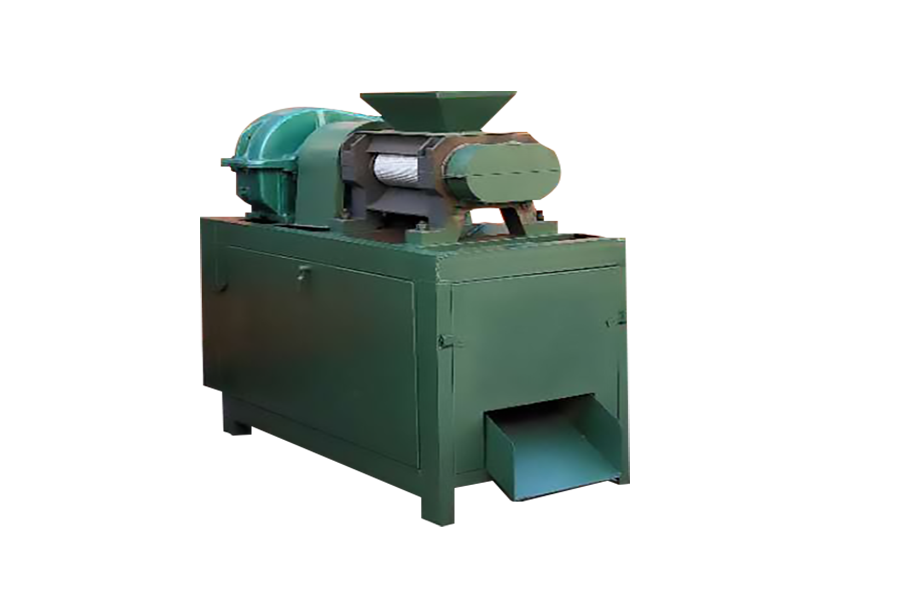
Double Roller Extrusion Granulator
- Output (kg/h): 5000
- Voltage: 380/400/440/600
- Dimension(L*W*H): ACCORDING TO DRAWING
- Usage: Producing NPK Compound Fertilizer Granules
- Raw Material: Compound Fertilizer
- Applicable Industries: Manufacturing Plant, Farms, Construction works, Energy & Mining
- Core Components: PLC, Engine, Bearing, Gearbox, Motor, Pressure vessel, Gear, Pump
Get Price Now!
Description
Forklift FeederThe double roller extrusion granulator is the key equipment for compound fertilizer granulation. It has advanced technology, reasonable design, compact structure, novel and practical, low energy consumption. It is matched with corresponding equipment to form a small fertilizer production line, which can form a continuous production capacity, mechanized production.
We use eugenic formula when manufacturing the Double Roller Extrusion Granulator for Sale, no drying, normal temperature production, the product is rolled and formed at one time, so that the product quality meets the requirements of compound fertilizer technical indicators. It is a high, medium and low concentration special compound fertilizer and compound fertilizer industry for the production of various crops Energy-saving and consumption-reducing replacement products.
Compact structural design of the roller presses granulation equipment
The whole machine is divided into four parts:
- Rack part: All the working bodies of the machine are installed and fixed on the rack. The frame of the machine is made of medium carbon steel plate and channel steel welded, and through strict quality control and specific process requirements, the purpose of this machine is achieved. Used in loading and unloading transportation.
- Transmission connection part: The motor drives the pulley, the V-belt and the reducer to drive the machine head to work. In addition, the sprocket and the chain form the transmission chain and transmit it to the crushing and separation working part. Among them, the transmission reducer and the working part of the machine head are meshed with nylon pin couplings to transmit and drive.
- The working part of the machine head: the transmission wheel is transmitted to the transmission roller shaft through the pin coupling. The synchronous operation of the pair of rollers is guaranteed by a pair of open wheels. There are specific bearings on both sides of the active and passive shafts, which are composed of bearing frames and installed. on the rack.
- Crushing and separation working part: After the material is squeezed by the roller, it flows into the crushing chamber on the lower side, and the ball material and the return material can be separated by the rotation of the double-shaft mace.
How to make npk granules with the double roller extrusion equipment?
This series of roller granulation is an extrusion slip model. Its working principle is: the belt and pulley are driven by the motor, transmitted to the driving shaft through the reducer, and synchronized with the driven shaft through the split gear to work in opposite directions. The material is added from the feeding hopper, extruded by the rollers, demanded into balls, and passed through a pair of chains, sent to the crushing screen working room, screened and separated the finished particles (balls), and then the returned material is mixed with the new material, granulate again. With the continuous rotation of the motor and the continuous entry of materials, mass production can be realized.
Technical Parameters for the double roller dry powder granulator equipment
In this series of granulators, the shape and size of the ball socket on the roller skin can be selected according to the needs of users, and there are a wide range of choices. Spherical and square shape. At present, they are all in the shape of a flat sphere.
Model | Power | Granular sizes | Roller Dimensions | Dimensions |
DGZ-1T | Ggranular sizes≤4.5mm:11kw.Ggranular sizes>4.5mm:15kw. | 3-10mm | Ø150*220mm | 1450*800*1450mm |
DGZ-1.5T | Ggranular sizes ≤4.5mm:18.5kw.Ggranular sizes>4.5mm:22kw. | 3-10mm | Ø150*300mm | 1450*850*1500mm |
DGZ-2T | Ggranular sizes ≤4.5mm:22kw.Ggranular sizes>4.5mm:30kw. | 3-10mm | Ø185*300mm | 1630*850*1650mm |
DGZ-3T | Ggranular sizes ≤4.5mm:37kw.Ggranular sizes>4.5mm:45kw. | 3-10mm | Ø300*300mm | 1850*1100*2050mm |
Advantages of the extrusion granulation equipment for sale:
- Energy saving and consumption reduction Extrusion granulation is the granulation of materials at room temperature. Compared with other methods, drying measures such as fuel oil and gas are not required.
- There is no need to add additional binders. The commonly used production method of compound fertilizer in China is steam granulation. After the water vapor condenses and crystallizes between the material molecules, it acts as a binder during the manufacturing process. However, in the drying process, the water inside and on the surface of the particles must be driven out, otherwise the fertilizer will be easy to stick and agglomerate during storage. While dry granulation does not require additional additives, it only needs to use the intermolecular force of the material itself, which simplifies the process and reduces energy consumption.
- Low investment Because the drying process is omitted, and the ratio of return material is low (accounting for about 15% of the total feed amount of the extruder), the process flow is simple and the investment is low.
- Flexible raw material composition Extrusion granulation has a wide range of raw material routes. There are more than 20 kinds of materials that have been successfully used in extrusion granulation: ammonium nitrate, urea, ammonium chloride, calcium nitrate, potassium chloride, potassium sulfate wait. In addition, the extrusion granulation process can flexibly change product formulations in a very short time, and a set of devices can produce products with more than 30 formulations.
- Green environmental protection without three wastes discharge, extrusion granulation consumption capacity, only electricity, environmental protection without three wastes discharge, in line with the country’s basic national policy on environmental protection, but also in line with the development strategy of enterprise environmental protection.
Debugging and installation of the roller extrusion granulator
- Debug
Adjustment of roller gap
In production, it is sometimes necessary to increase the output or increase the bite angle. At this time, the distance between the two pressing shafts can be increased, and the distance between the driving shaft roller and the passive shaft can be increased. The steps are as follows: stop the machine and remove the passive shaft The two ends of the cover are pressed, and the two inner eccentric sleeves are rotated in the same direction, one position at a time, and the two rollers cannot collide with each other, and should be kept between 0.3-1mm.
Alignment adjustment of the ball socket
The ball socket is formed by the dimples on the main surface of the roller, so there are problems of axial alignment and circumferential alignment;
- Installation
- Axial alignment: It has been adjusted during installation. Generally, it is unlikely to be adjusted. When adjustment is required, tighten or loosen the glands on both sides of the passive bearing seat, thereby promoting the displacement of the eccentric sleeve and the driving shaft. corresponding to the rollers.
- Circumferential alignment: The steps of circumferential alignment are as follows: Loosen the 6 consecutive bolts of the driven gear and the adjusting sleeve, so that the adjustment and the driven gear are slightly disengaged. Since a ball and socket adjustment amount has been tested in the design, and is equipped with two adjustment bolts, so the dislocation can be adjusted no matter how much the dislocation is.
- Because the ball socket is too small, the carton board is placed between the two rollers during adjustment. After rolling, each project must have a process. The same is true for the organic fertilizer equipment, which is completed by step-by-step installation, so Inevitably there will be some steps, which is a process that must be taken.
3. Â Circumferential Alignment
The steps of circumferential alignment are as follows: Loosen the 6 connecting bolts between the passive gear and the adjusting sleeve, so that the adjusting sleeve and the passive gear are slightly disengaged. Since the design has set – a ball and socket adjustment amount, and is equipped with two Adjusting the bolts, so no matter how much the misalignment is, it can be completely misaligned. Because the ball socket is too small, the carton board is placed between the two rollers during adjustment. After rolling, it can be seen whether the adjustment has achieved the purpose. Generally, the passive shaft roller should be a quarter ahead of the driving shaft roller. After alignment, 8 bolts can be tightened.
  4. Precautions for the operation of the roller extrusion granulator
- The machine should be started without load, and it is strictly forbidden to start with material.
- It is strictly forbidden to enter the material with iron, so as not to break the roller shaft.
- Dry yellow oil should be applied to the gear before starting the machine.
- Apply yellow and dry oil to the chain and sprocket every 7 days.
- The bearing seat should be played once every three months or replaced with new yellow dry oil.
- The gear oil must be added once before the reducer can be used for production, and the gear oil must be replaced every four months.
Get a Free Quote with Detailed Price Lists, Inquiry Us Now